超凡智能VISI软件引领设计革新新浪潮
19429202025-03-23安卓软件9 浏览
传统模具设计,是否已迎来“智能革命”?
模具设计行业长期面临一个争议性问题:传统设计流程依赖人工经验,效率低、门槛高,而高端软件又价格昂贵、操作复杂。这种矛盾下,中小型企业如何在保证质量的同时实现降本增效?超凡智能VISI软件引领设计革新新浪潮,或许正在给出答案。
1. 效率瓶颈:人工经验能否被智能工具替代?
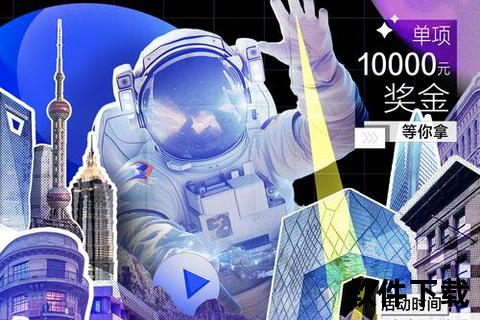
传统模具设计依赖工程师手动建模、反复修改,耗时长且易出错。例如,某小型模具企业曾因设计误差导致模具返工,项目周期延长30%。而VISI软件通过无参数化设计模式,简化了操作流程。其混合建模技术(结合曲面与实体)允许设计师快速调整模型结构,无需从零开始。
案例支撑:浙江一家汽车零部件厂商引入VISI后,设计周期从14天缩短至7天,人工干预减少40%。软件内置的自动检测功能可识别干涉和壁厚不均问题,避免了90%的返工风险。
这种“半自动化”模式并非完全取代人工,而是将重复性工作交给系统,让工程师专注创意与优化。超凡智能VISI软件引领设计革新新浪潮的关键一步,正是通过工具升级释放人力价值。
2. 复杂曲面:建模难题能否“一键破解”?
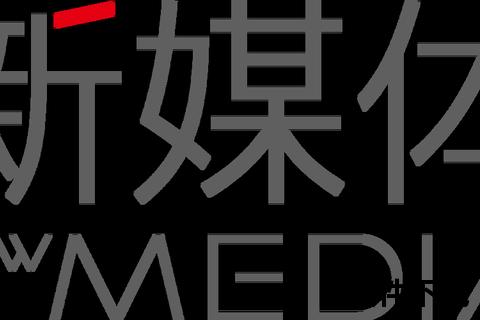
曲面建模是模具设计的核心难点,尤其对家电、消费电子等外观要求高的行业。传统软件如UG虽然功能强大,但对硬件要求高,且操作复杂。VISI则通过针对性优化,在保证精度的同时降低技术门槛。
案例支撑:深圳某手机外壳模具厂采用VISI的“快速分模”功能,将原本需要5天完成的复杂曲面分模压缩至8小时。其塑模设计模块(Visi-Mould)可自动生成滑块、冷却水道等结构,并通过模流分析(Visi-Flow)预测填充缺陷。VISI 2024版本新增智能修复工具,可自动修补模型缝隙,修复效率提升60%。
从手动调整到系统辅助,超凡智能VISI软件引领设计革新新浪潮的实践价值在此凸显——复杂问题不再依赖“技术大牛”,而是转化为标准化流程。
3. 制造断层:设计与加工如何无缝衔接?
设计与制造的割裂是行业痛点。设计师输出的模型常因格式转换或参数丢失,导致加工阶段需重新编程。VISI的整合型CAD/CAM系统则打通了这一环节。
案例支撑:江苏一家压铸企业使用VISI的CAM模块,直接将设计模型转换为五轴加工代码,编程时间减少70%。其加工策略库支持2-2.5D钻孔、3D轮廓铣削等,并可模拟刀具路径,避免碰撞。更值得关注的是,软件提供“云端协同”功能,设计团队与工厂可实时共享数据,迭代效率提升50%。
这种端到端的解决方案,不仅缩短了交付周期,更让设计与制造团队“说同一种语言”。超凡智能VISI软件引领设计革新新浪潮,正推动行业向数字化协作迈进。
未来建议:企业如何拥抱智能设计?
1. 按需选型:小型企业可优先采用VISI基础版,低成本实现效率跃升;大型企业可结合UG等软件,发挥VISI在分模和加工环节的优势。
2. 人才转型:培训工程师掌握智能工具的逻辑,而非单纯操作技巧。例如,学习如何利用VISI的模拟结果优化设计方案。
3. 生态整合:将VISI与ERP、PLM系统对接,构建从设计到生产的完整数据链。
工具的革新从未停止,但核心始终是“人机协同”。当企业不再纠结于软件之争,而是聚焦如何让技术赋能创意,这场超凡智能VISI软件引领设计革新新浪潮,才能真正转化为生产力革命的基石。