极致突破ADAMS软件革新多体动力学仿真效能巅峰
19429202025-03-22电脑软件20 浏览
<>
在工业设计领域,多体动力学仿真是验证机械系统性能的“数字试验场”。随着产品复杂度飙升,传统仿真工具常面临两大争议:效率与精度的矛盾是否无法调和? 面对汽车悬架、航天器部件等复杂系统,工程师不得不在建模耗时、计算资源消耗与结果可信度之间反复权衡。这一困境下,极致突破ADAMS软件革新多体动力学仿真效能巅峰的技术路径,正引发行业对仿真范式变革的深度思考。
1. 复杂系统建模如何兼顾效率与精度?
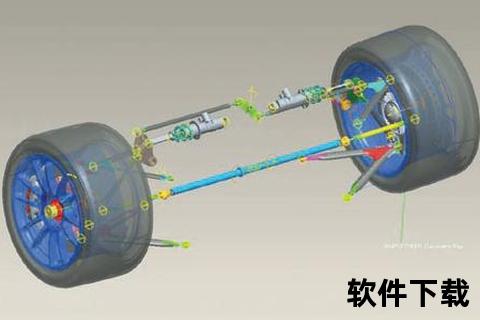
传统多体动力学建模需手动定义每个部件与约束,耗时长且易出错。以某车企研发新型电动汽车悬架为例,工程师需在ADAMS中构建包含柔性车身、液压减震器与控制系统耦合的模型。通过极致突破ADAMS软件革新多体动力学仿真效能巅峰的参数化模板技术,悬架几何参数、材料属性与载荷条件被封装为可复用的模块,建模时间从3周缩短至2天。
更关键的是,ADAMS/Flex模块支持导入有限元软件生成的.mnf文件,自动剔除对振动影响小的模态。某航空发动机叶片仿真案例显示,柔性体模型自由度从12万降至800,计算速度提升40倍,且应力分布误差控制在5%以内。这种“智能降维”技术,让复杂系统的高效建模不再是“削足适履”。
2. 大规模计算如何突破性能瓶颈?
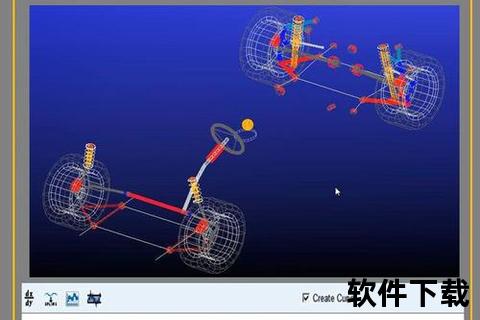
当仿真对象扩展至整机系统时,计算资源往往成为瓶颈。ADAMS的破局之道在于多核并行求解器与实时仿真技术。以火星车地形通过性测试为例,传统单核求解需72小时完成6种地貌的动力学分析。而ADAMS 2025版C++求解器利用GPU加速,将计算时间压缩至8小时,且支持实时调整坡道倾角与轮毂扭矩,动态验证控制算法。
另一突破来自与Marc软件的联合仿真。某重型机械臂作业时,液压驱动与结构变形高度耦合。通过ADAMS-Marc协同计算,机械臂末端轨迹误差从12%降至3%,同时捕捉到传统刚体模型无法识别的谐振点。这种“刚柔耦合+多物理场”的集成能力,让极致突破ADAMS软件革新多体动力学仿真效能巅峰成为可能。
3. 多学科协同如何实现数据闭环?
现代产品开发需要机械、控制、材料等多学科协同,但工具链割裂导致数据孤岛。ADAMS/Controls模块的双向联合仿真接口解决了这一难题。以自动驾驶底盘开发为例,控制算法在MATLAB/Simulink中设计,机械模型在ADAMS中运行,两者通过实时数据交换实现闭环验证。某厂商数据显示,联合仿真将标定周期从6个月缩短至45天,且避免了3次物理样机碰撞风险。
更前沿的探索体现在与Isight的深度集成。通过将ADAMS模型嵌入Isight优化流程,某风力发电机叶片设计团队在2000次迭代中筛选出最优气动-结构参数组合,发电效率提升18%,而人工调参时代同等成果需耗费2年。这种“仿真-优化-再仿真”的智能闭环,重新定义了多体动力学工具的价值边界。
<结论>
对于希望驾驭极致突破ADAMS软件革新多体动力学仿真效能巅峰的工程师,建议采取三步策略:
1. 模块化建模:优先使用Adams/Car、Adams/Controls等垂直行业模板,减少重复劳动;
2. 混合计算策略:对关键部件采用柔性体建模,非核心区域保留刚体假设,平衡精度与速度;
3. 生态协同:通过Isight、MATLAB等工具构建自动化流程,将仿真从“单点工具”升级为“决策中枢”。
正如某航天机构在卫星展开机构仿真中验证的当建模效率提升60%、计算资源消耗降低75%,工程师才能将创造力集中于真正的创新设计——这才是仿真技术革命的终极意义。